QMS – Quality Management System
5 Reasons Why You Need to Implement a QMS
A Quality Management System is more than just a strategy for enhancing business processes; it’s a fundamental approach to aligning your operations with quality and regulatory standards, ensuring customer satisfaction, and fostering a profitable business. It establishes a framework for how you do business.
- It establishes your company processes to aligns with regulatory expectations.
- It defines a framework for how you do business.
- It aligns expectations and deliverables for key processes.
- A QMS is critical for building a foundation for quality, environmental, and risk management in your company.
- For many businesses, having a QMS is a requirement – it is not optional.”
A QMS acts as the backbone of your company’s operational framework, focusing on consistently meeting various requirements. It establishes your company processes in a way that aligns with regulatory expectations.
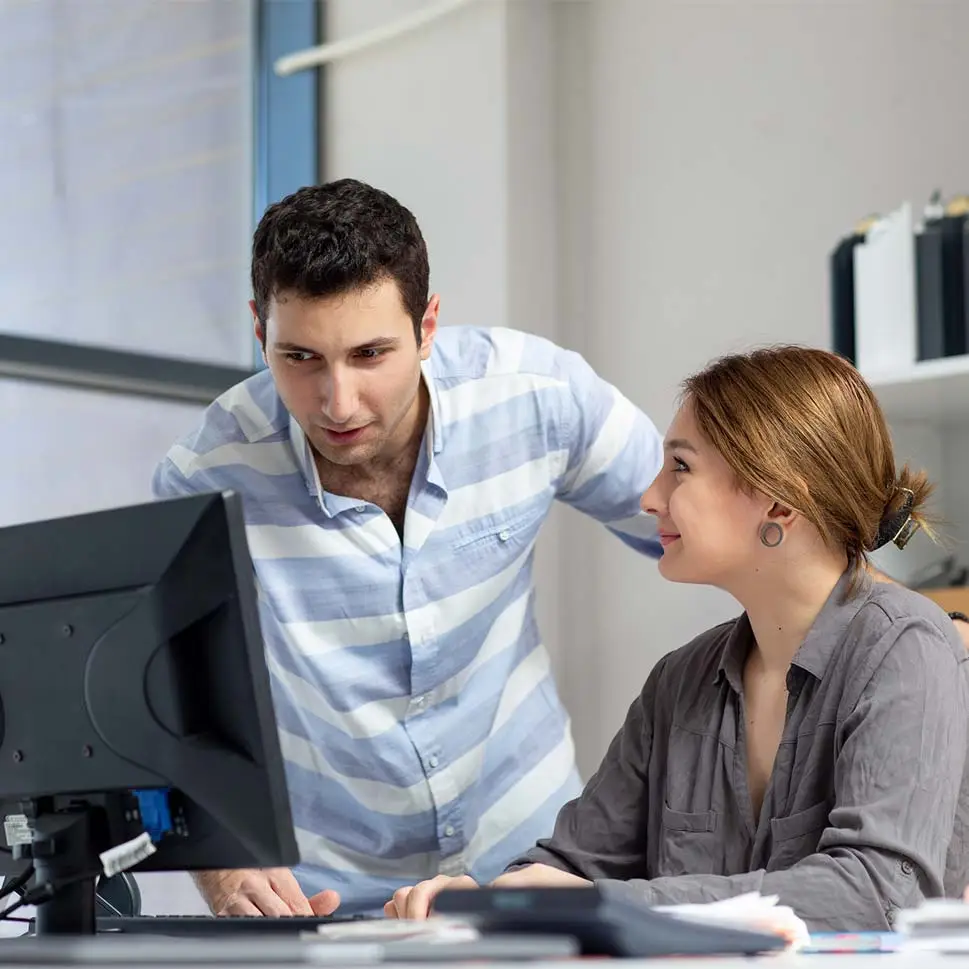
2. QMS is a Framework
The overall purpose of establishing a QMS is to establish the framework and requirements of standards and legal requirements. Your QMS establishes your company processes. Your company rules. Your company expectations. How you do things. What documents and records you generate.
3. QMS Defines Expectations & Deliverables
Building your QMS early has 3 primary advantages.
- Your QMS framework sets the expectations and lays the ground rules for your resources.
- You start generating critical documents and records as objective evidence to support decisions and submissions.
- The QMS processes define what documentation is required and who need to review and approve documentation.
When QMS is required
Companies need to be authorised by the government before they can undertake plumbing, gas, sewage or electrical installations. To gain that authorisation, they must have an approved quality management system (QMS).
Choice of QMS and Control Authority
Before you can apply for authorisation, your QMS must already be fully developed and have received preliminarily approval from one of the approved control authorities, which you can find listed on the Safety Authority’s website (https://www.sik.dk/en/business/legislation/authorisation/executive-order-quality-management-systems)
Approval Process
When the control authority approves your QMS, it forwards the preliminary approval to the Safety Authority. Once it has been approved by the Safety Authority, you can officially apply for authorisation. After approval by the Safety Authority, you must have a control visit within the first year and renew your approval every second year.
It is important to arrange audits with your control authority to avoid periods without authorisation. If the new approval is issued 3 months before the expiration of the old one, it is valid from the start of the expiration date of the old one. If your company operates in multiple sectors (plumbing, gas, etc.) each requiring authorisation, you can use one QMS for all of them, but you must have approval for each sector.
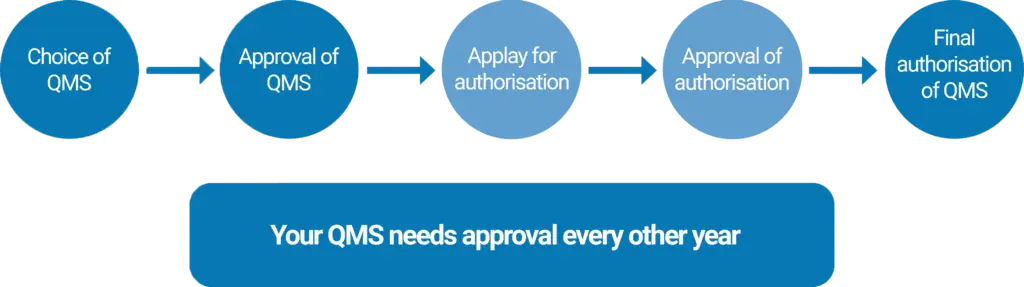
Contents of your QMS
Your company’s QMS should include:
- Company data, including company name, CVR information and address.
- An organisational chart, with the names and roles of relevant
- Responsibilities, competencies and authorities of employees.
- Documentation for the professionally responsible person approved by the Tax Authority.
- Description of the
- Management review and a plan to improve any deviations found during the last audit.
Your QMS should also describe how your company and the professionally responsible person ensure for each project that there is
- Proper staffing
- Adequate instruction
- Final control and verification
- Supervision of the work
For a more detailed guide, see the Safety Authority’s guidance here.
Why does my business need a QMS?
Projects within the electrical, plumbing, sewage and gas sectors often involve numerous complex tasks and processes that require meticulous management and monitoring. Your QMS plays a central role in ensuring that your employees are operating effectively and abiding by the strictest standards and requirements.
Electrical Work
The requirements within the electrical field include ensuring that electrical systems and installations are reliable. This involves compliance with national and international electrical standards, proper maintenance and documentation of electrical systems, and addressing energy efficiency and safety.
Plumbing and Heating Work
QMS requirements for plumbing and heating focus on ensuring that plumbing installations and appliances comply with environmental, energy efficiency and quality standards. This encompasses water quality, wastewater management and the sustainability of water and heating supply systems.
Sewage Work
QMS requirements for sewage are centred around the regulation and control of sewer systems to prevent pollution and environmental damage. This involves inspection, maintenance and documentation to ensure the integrity of the systems and compliance with regulations.
Gas Work
QMS requirements in the gas sector involve ensuring the safety of gas and distribution systems to prevent leaks, hazards and pollution. This requires compliance with strict regulations and standards and extensive documentation of inspection and maintenance work.
For companies within the electrical, plumbing, sewage, and gas sectors, it is crucial to implement a well-functioning QMS that meets the industry’s requirements. This is not only to provide reliable services but also to create a high degree of credibility and trust among customers and partners.
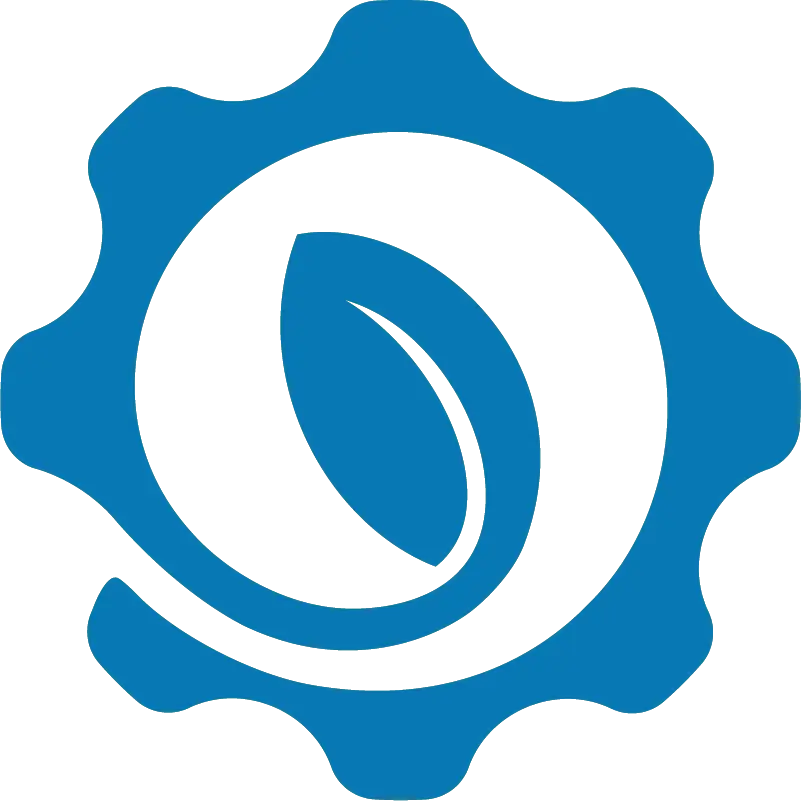
BMF as a QMS
BMF has been successfully implemented as a QMS in companies that have subsequently been certified by recognised certification bodies such as Bureau Veritas Certification. BMF is an extension to SharePoint within Office 365, which makes it easy and secure to use as a management system.
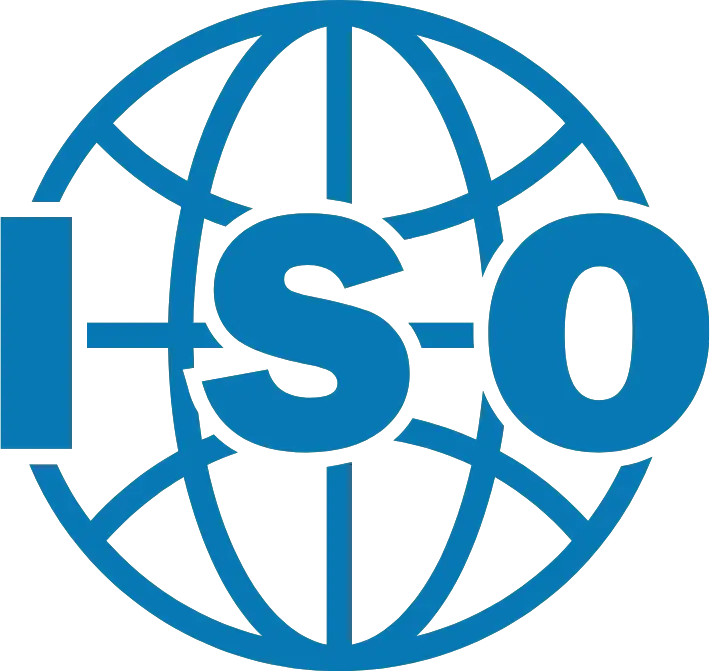
QMS vs. ISO Certification
If your company wishes to become ISO certified, for example, ISO 9001:2015, the ISO certification can replace your QMS, provided that it covers your specific business sector. BMF can also assist with ISO certification while simultaneously being a platform for managing documents, risk management and incident reporting to meet ISO requirements.
When I check with Google, I find things like “ISO 9001 is a Quality Management System (QMS)”, so it seems confusing to say that ISO can replace QMS. Please clarify.